Grooved Beaded Heaters
Grooved beaded heaters are intended for mass installation into ovens of cookers for households.
Grooved beaded heaters are an alternative to the bottom tubular heater in the oven. Compared to a tubular heater of the same power and length, it has a better (lower) specific load per unit of the heater surface (8W/cm2), which enables a longer service life.
The heating spiral is insulated along its entire length with ceramic rings - beads - and is inserted into a longitudinally ribbed groove made from hot-dip aluminised tin.
The shape of the heater can be adjusted according to the customer’s requirements to ensure the best energy economy and baking quality.
Technical Characteristics of Heaters
The heater is made from a heating spiral that is insulated along its entire length with ceramic rings - beads. The quality steatite ceramics ensure good insulation at operating temperatures (outlet current). Low specific load of the heating spiral ensures equal heat distribution during baking.
The heater is inserted into an open, longitudinally ribbed groove from aluminised tin. The aluminised tin remains firm at temperatures up to 850 °C due to the interaction of the steel core with the aluminium coating and gives off the heat with a reflection effect.
The heater is fastened to the bottom side of the oven longitudinally or transversally across the galvanised flange. The groove is linked with the framework with crossbars made of materials that are not impacted by the effects of the environment.
The power of the heater per unit of the groove length does not exceed 8W/cm, which is important for ensuring the long service life of the heater.
Heaters Types
Voltage
|
Power
|
Marking
|
230V
|
1100W
|
GP1125, GP1123, GP1127, GP1128
|
400V
|
1100W
|
GP3125, GP3127, GP3128
|
230V
|
900W
|
GP1127-K
|
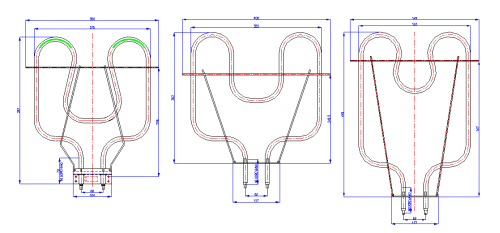
Quality
The heaters are environmentally friendly and simple to recycle.
They are made in accordance with ISO directives. They comply with RoHS requirements and have VDE approval for production and the use of the VDE mark.
The production process is monitored with statistical process control (SPC) and the failure mode and effects analysis technique (FMEA) and is also fully computer aided. This makes it possible to achieve extremely high quality products.